Project Report: Flow Capacity Weighing and Dosing in the Process of Grain Handling at the Grand Harbour of Malta
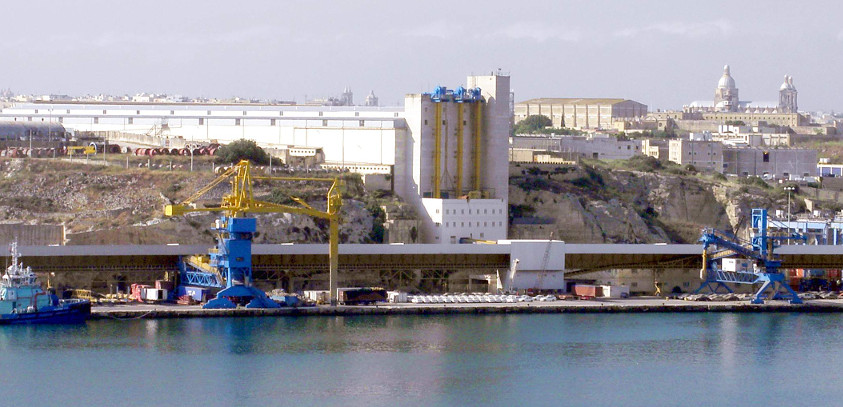
The Task
Three existing grain handling weighing systems which were originally supplied by Bühler- Miag and Molenschot (see details at www.kordingrain.com.mt) have to be equipped with weighing and dosing technology for modernisation purposes. A high weighing accuracy at high dosing and flow rates must be achieved. The different flow characteristics of the different grain varieties are to be considered. All major operations have to be automated. The data acquisition and data processing need to be expanded and an extensive logging must be ensured. The operation must be simplified in spite of the complexity of the system and adapted to the new requirements. Any additional customer specific requirements have also to be considered. The normal grain handling operation must not be in any way interrupted during the conversion of the systems.
The Büttner Concept
-
The three existing mechanical hybrid hopper scales (for ship unloading: capacity 10
tons; for ship and truck loading: capacity 2 x 5 tons) are being converted. The load shall
be applied on four weighing modules, model B-DJ-M5, (for ship unloading: 4 units each
of 10 tons capacity; for ship and truck loading: 2 x 4 units each of 4.7 tons capacity).
-
A load cell junction box, model AK, is assigned to each scale, with the load cells being
connected in parallel. Screened cables connect the junction box with the data
acquisition electronics. For the data acquisition a certified weighing indicator, model
R420 (model R320 also suitable), is provided for each scale. The measured values are
then being passed on to the weighing and dosing amplifiers, model PE1367 with
integrated controllers, which have been modified for this application. The main
controller, model MC-XS, which is used for the data input and data display and which
also controls basic operation functions, provides the connection to a standard Windows
personal computer via serial interface RS232/485.
-
Each of these Windows computers (an autonomous computer for every scale) is
equipped with a newly developed observing and controlling software for comfortable
scale operation control. Main features of this user software are the data input (also of
scale parameters, setpoints, flow rates, material parameters, ship/truck data, etc.), the
sequence control (ship unloading, ship loading, truck loading, ship-to-ship transfer,
storage silo-to-silo transfer), the graphical visualisation of the scale operations and
display of status information, the monitoring of pre and post bins, and of course, the
ability to log and print different reports.
-
The control of the pneumatically operated filling and discharge flaps/gates is done with
potential-free relay contacts, which are in the downstream from the weighing and dosing
amplifiers, model PE1367 and the main controller MC-XS. The signals of various
feedbacks (e. g. closed gates, subsequent reservoir full, empty hopper, no air pressure
available, etc.) are being passed on to the respective scale control system through this
device, too.
The Implementation
Because of the critical importance of the systems for the basic supply services of the whole island (the only facility of its kind in Malta) both the mechanical conversion of the weighing bins and the installation of the control systems had to be carried out in planned stages. The system had to remain operational during the entire modernisation process. As a first step, the scales were successively converted, the old mechanical hybrid devices of the scales were removed, and the weighing bins were put on weighing modules, model B-DJ-M5. For a short time the new load cells worked together with the old scale control systems, until all installations were completed, and the operation could be switched over entirely to the new control systems.
The Commissioning (with Test Run)
The commissioning was performed by a team consisting of engineers and technicians from the company's headquarters in Esslingen (www.gbuettner.de) and the subsidiary in Malta (www.buettner-malta.com), in close collaboration with the technicians of the customer. Even during the commissioning newly expressed enhancements to the software requested by the customer were implemented in the user software. The individual adjustments and fine tuning took up most of the time, this obviously being the most important part of commissioning. The operators were extensively instructed. Details were also discussed to provide immediate assistance in case of an emergency. Test runs under various possible conditions (different flow properties of the materials, special features of ship unloadings, etc.), and eventual possible faults were simulated and eventually successfully executed on site. Valuable feedback was continuously requested and ably supplied by the customer whose total collaboration was evident throughout the whole project.
The Test Mode
A test run over several weeks was agreed. During this time, the customer gained experience with the new systems and at the same time provided necessary information to help optimise and enhance the system. Further extensions, which were not known at the ordering stage, as well as other improvements in the areas of automation and reliability were incorporated during the test phase. A closing meeting held after the end of the test operation confirmed the acceptance of the new plant by the customer.
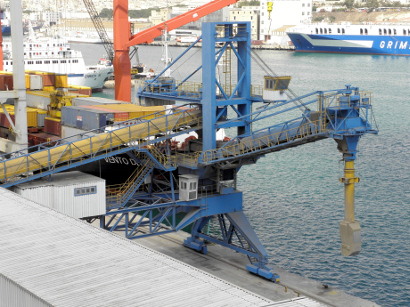
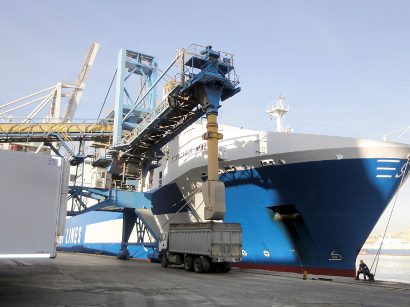
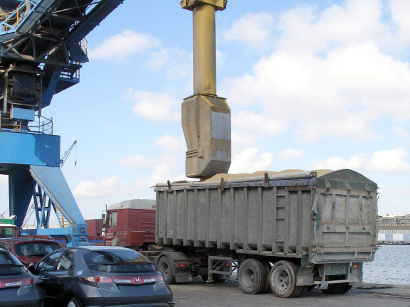
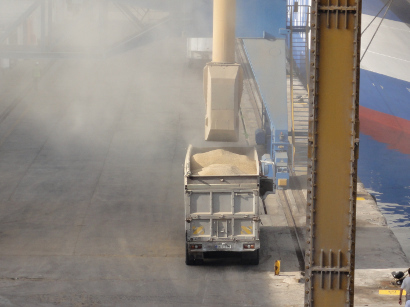
The Achieved Goals
The old mechanical hybrid scales of Bühler-Miag/Molenschot were successfully converted, modernised and put on Büttner weighing modules. Through the customised user software, our weighing and dosing control systems can achieve a high degree of automation on all three systems. The operational sequences of ship unloading, ship loading, truck loading, ship-to-ship transfer, storage silo-to-silo transfer (silo contents relocation), silo filling and silo discharge were optimised. Increases on the flow rate by about 15% compared to the old system, a much higher accuracy (better than required), the inclusion of additional external signals and clearly arranged on-screen visualisation of material related data, operation sequences and commercial details, together with a comfortable data specification and data processing with extensive logging opportunities even exceeded expectations.
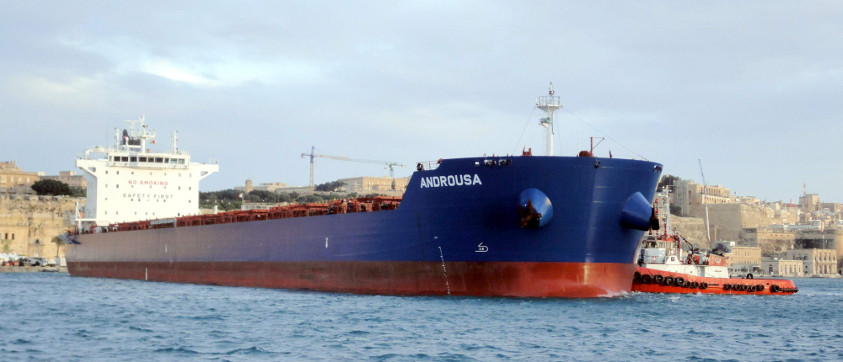
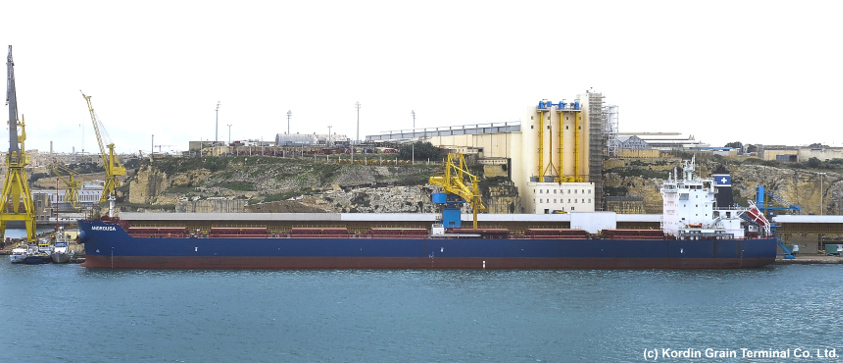
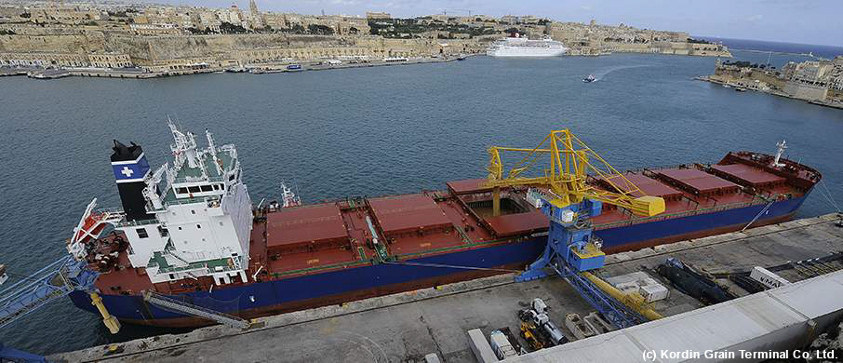
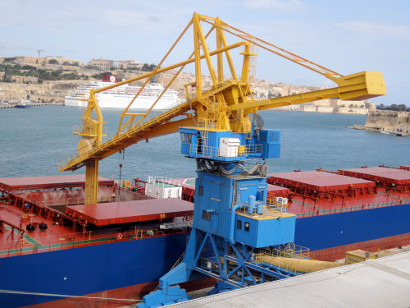
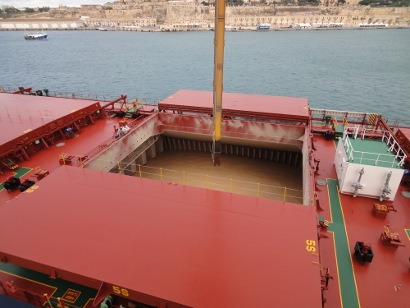
Closing Remarks
The project's success is the result of the customer's requirements, experience-based proposals, well planned project management, the conscientious performance of work, as well as the continuous flow of information between client and Büttner throughout the execution of the project. Of course, the reliability and accuracy of the technology used is a major building block for success. Customers quickly recognise both the technical advantages of the new systems and the ease of use in connection with the convenient user-friendly software. We thank Kordin Grain Terminal Co. Ltd. for their unstinting collaboration in this project and for agreeing to the publishing of this article, and for the contribution of various photos.